The label is a printed product used to indicate the relevant description of the product. Some are self-adhesive on the back, but some printed products are not adhesive. The label with adhesive is known as the "self-adhesive label".
Self-adhesive label is a kind of material, also called self-adhesive self-adhesive material. It is a composite material with paper, film or other special materials as the fabric, coated with adhesive on the back, and coated with silicon protective paper. Self-adhesive is a general term for materials with such properties.
The Development Process, Current Situation And Application Of Stickers
The label material was invented by American R-Stanton-Avery in the 1930s. Mr. Airy invented the first coating machine and began to mechanize the production of label. Compared with traditional labels, self-adhesive labels do not need to be glued or pasted, and are easy to store and can be used quickly and easily in many fields. Soon, self-adhesive labels have spread to all parts of the world and developed a number of Category!
China began to print adhesive labels in the late 1970s. Most of the equipment and technology came from Japan. Initially, it was mainly in the low-end market. With the development of society and the improvement of awareness, labels are very popular. It soon occupied a large area of packaging in the middle and high markets. There are thousands of domestic private enterprises engaged in the printing of self-adhesive labels, which greatly promoted the development of the industry!
In market research, the number of labels per capita is usually used to assess the market prospects. According to data from relevant media, the average annual consumption for Americans is 3-4 square meters, and the average annual consumption for Europeans is 3-4 square meters. Japan The annual consumption per capita is 2 ~ 3 square meters, while the annual consumption per capita in China is 1 ~ 2 square meters, which also means that there is still much room for development in China!
There is an increasing demand for high-end labels in the market. Various types of high-end labels can be processed in China. Labels previously processed abroad have gradually been converted to domestic production, which is also one of the main reasons for the rapid development of domestic label printing.
Application of labels
As a form of packaging that achieves appearance and specific functions, self-adhesive labels can be flexibly applied to all walks of life. At present, the label has excellent applications in the pharmaceutical industry, supermarket logistics industry, electronics industry, lubricants, tire industry, daily chemical, food, clothing and other industries!
There are two types of labels: one is paper-based labels, and the other is film-based labels.
1) Paper Labels
Mainly used in liquid washing products and popular personal care products; film materials are mainly used in high-end daily chemical products. At present, popular personal care products and household liquid washing products in the market account for a large proportion, so the corresponding paper materials are used more.
2) Film Labels
Commonly used PE, PP, PVC and other synthetic materials. The film materials are mainly white, matt and transparent. Since the printability of the film material is not very good, it is generally corona treated or added with a coating on its surface to enhance its printability. In order to prevent some film materials from being deformed or torn during printing and labeling, some materials will also undergo directional treatment to be unidirectionally stretched or biaxially stretched. For example, BOPP materials that are biaxially stretched are quite common.
The structure of the label
In a general sense, we call the structure of the label a "sandwich" structure: face material, glue (adhesive), and base paper. These three-layer structure is the basic structure, which is also visible to the naked eye.
In fact, many materials may be more finely divided. For example, some film surface materials have a coating on the surface, which is easy to print, and some materials and glue are also coated, so that the material and glue can be fully combined.
Production process of label
To put it simply, the manufacturing process of adhesive label materials is completed by coating and compounding two processes. There are usually two types of equipment, namely, split type and tandem type. According to different products or different output requirements, choose different equipment.
In the whole production process, there are many details that need to be focused on, which will directly affect the subsequent use of materials, including:
1. The weight of the base paper coated with silicone oil (there are also special bottom paper manufacturers);
2. The weight of glue coating;
3. Drying the glue;
4. Rewetting treatment in the coating process;
5. Uniformity of coating;
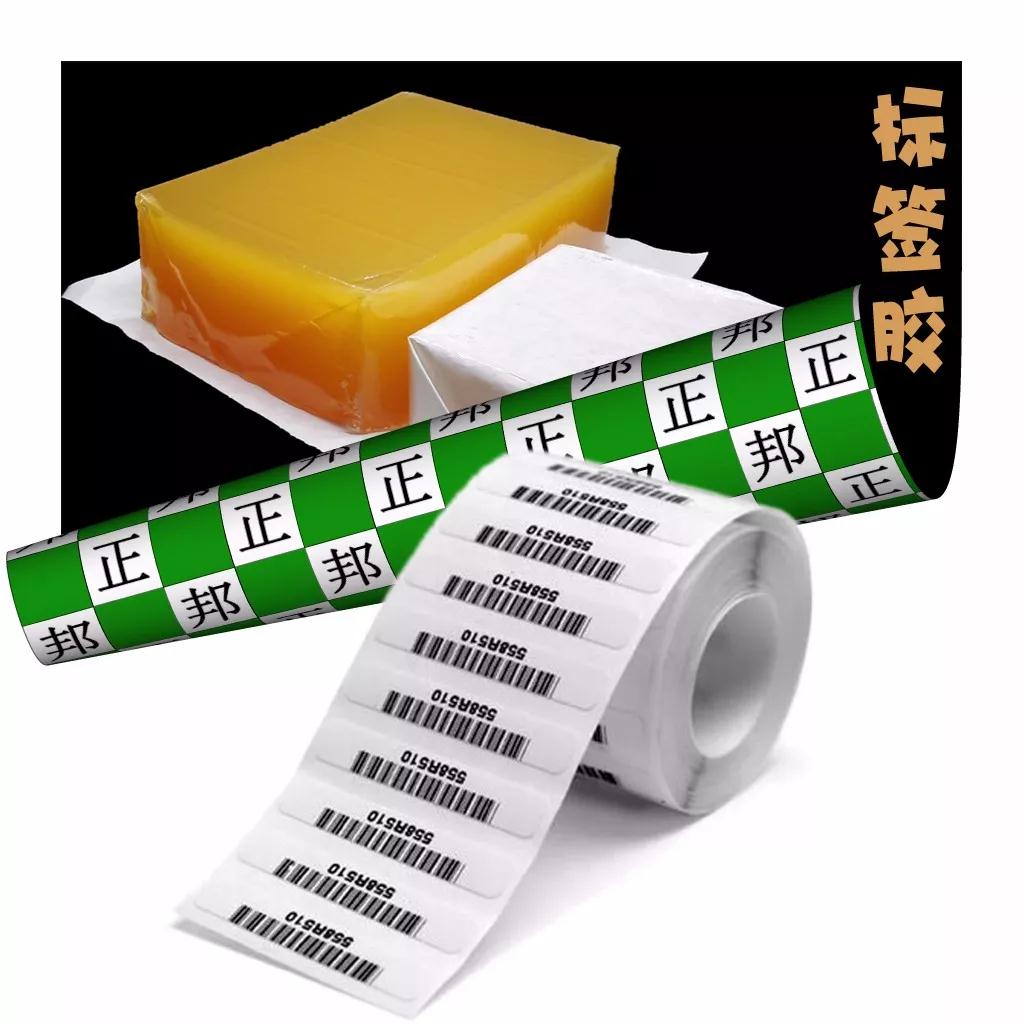
Label Material Introduction
(1) Face material
1. Paper surface material
Mirror coated paper, coated paper, matt paper, aluminum foil paper, thermal paper, thermal transfer paper, etc. These materials can be directly judged by the naked eye or when writing simply;
2. Film surface material
PP, PE, PET, synthetic paper, PVC, and special film materials developed by some companies (Avery Dennis) such as Primax, Fasclear, GCX, MDO, etc. The film surface material has a unique effect, white or transparent or bright silver sub-silver and other methods of treatment, reflecting the colorful appearance.
Note: The development of types of surface materials is still in progress. The rendering effect of surface materials is closely combined with printing technology!
(2) Adhesives
A, according to the coating technology is divided into: latex, solvent adhesive, hot melt adhesive;
B. According to the chemical characteristics, it can be divided into acrylic (namely acrylic) and rubber-based;
C, according to the characteristics of glue is divided into: permanent glue, removable (repeatedly pasteable) glue
D, according to the consumer's perspective, it is divided into: general-purpose type, strong adhesion type, low temperature type, high temperature type, medical type, food type, etc.
Note: The choice of glue is determined according to the application of the label. There is no universal glue. The definition of glue is actually relative, that is, whether it meets the requirements of use is the decision plan.
(3) Backing paper
1. Glassine paper
The most used base paper is mainly used in web printing and conventional automatic labeling;
2. Plastic coated base paper
Often used when you need better flatness printing or manual labeling;
3. Transparent backing paper (PET)
There are many applications in the two fields. First, the surface material needs to have a high transparency effect; second, the high-speed automatic labeling.
Note: Although the backing paper will be "discarded" after use, the backing paper is a very important part of the label structure. The levelness of the glue level brought by a good backing paper, or the stiffness of labeling brought by a good backing paper , or the smoothness of the bidding brought by a good backing paper, are the key factors in the use of labels!
Precautions when applying self-adhesive materials
1. Choose self-adhesive materials
The following aspects need to be considered, such as: the surface condition of the object (the change in the surface energy of the object), the shape of the object surface, the labeling method, the labeling environment, the label size, and the final storage environment. Try labeling in small batches to confirm the final use effect (including selecting the appropriate material that can meet the printing requirements), etc.
2. Several important concepts
A, the minimum labeling temperature: refers to the lowest labeling temperature that the label can withstand when labeling, below this temperature it is not suitable for labeling; (this is when a laboratory is attached to the steel plate at the lowest temperature Value, but the surface energy of glass, PET, BOPP, PE, HDPE, etc. will change during the manufacturing process, so additional testing is required.)
B. Operating temperature: refers to the temperature range that can be tolerated when the label reaches a stable state after the labeling temperature is above the minimum labeling temperature for 24 hours;
C, initial tack: the tack generated when the label is fully contacted with the object to be attached is the initial tack;
D, final tack: usually refers to the tack displayed when the label reaches a stable state 24 hours after labeling.
(This article is reproduced from the Internet)